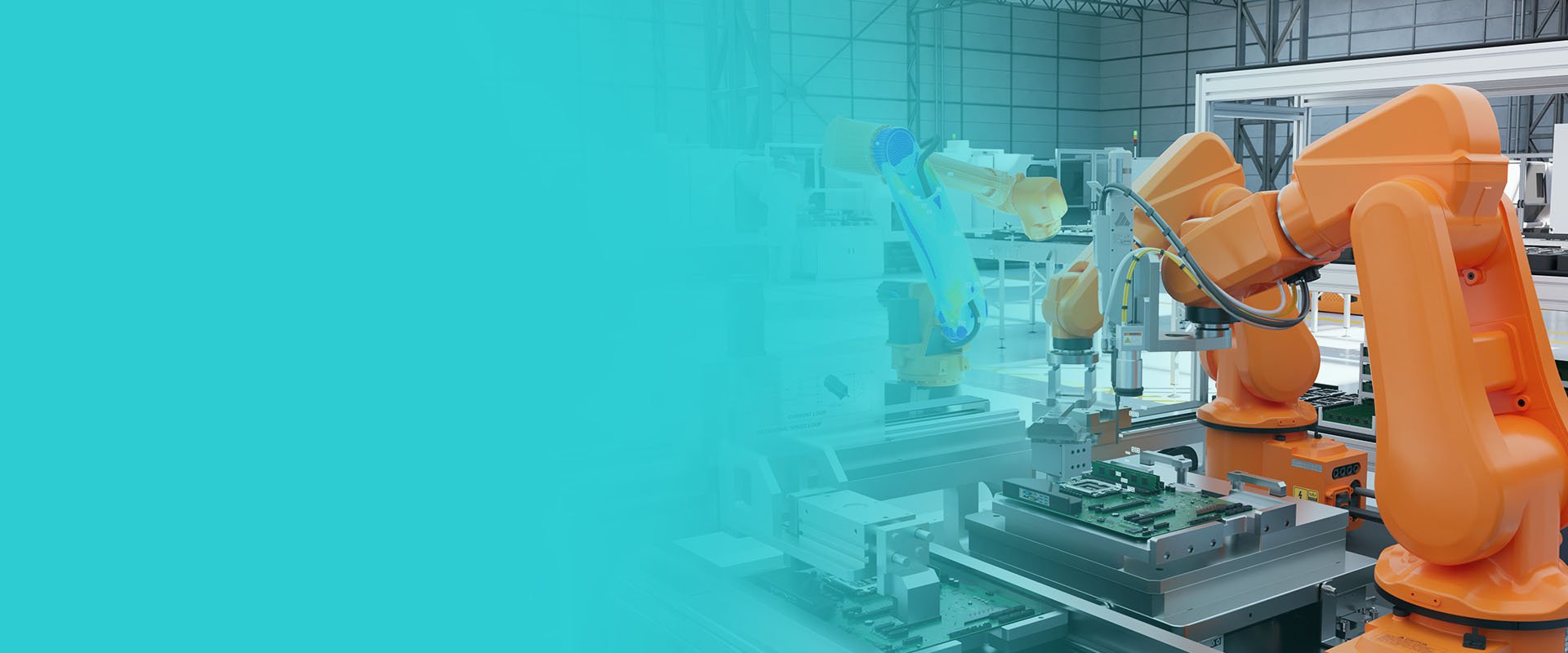
制造业重要的数字孪生技术解决方案
任何制造工艺的目标都是为了完善高质量产品的设计和实施。通过 Altair 全面的数字孪生解决方案(由业界值得信赖的仿真、人工智能(AI)、数据分析和 高性能计算(HPC)解决方案提供支持),企业将获得优秀的端到端能力,从而释放创新,节省时间,并最大限度地减少浪费。
Altair 的数字孪生解决方案通过虚拟调试、仿真技术、数字线程集成和实时资产管理为制造商赋能。通过运用虚拟调试和仿真能力,团队可以在制造系统建成之前就对其进行优化,降低成本并减少风险。此外,数字线程在整个产品生命周期中的无缝集成实现了实时的资产监控和管理,优化了维护计划,改善了设备。
Altair 在制造领域的数字孪生能力还包括轻量化、拓扑优化、 多物理场仿真、基于模型的开发等。寻找全球数字孪生的综合指南?请阅读 2022年 Altair 数字孪生全球调查报告。
制造业数字孪生洞察
了解我们的技术和专家如何启动您的数字孪生之旅。
联系我们制造业数字孪生中心
数字孪生的应用

Digital Twin for Sustainable Energy
Improving lifetime value of a fusion powerplant using a physics-based digital twin. Assystem is an international engineering and digital services group focused on low-carbon projects that accelerate the transition to clean energy. Assystem is committed to the development of decarbonized electricity (fusion energy, renewables and electricity grids) and clean hydrogen. The Assystem team wanted to leverage the expensive design models to create a digital twin by inputting the sensor data that was livestreamed from the plant, which helps engineers understand the plant's structural integrity and further optimize inspection and maintenance schedules.

Digital Twins Boost Barista - Altair® Helps Gruppo Cimbali Speed up Innovation and Go-to Market
As a key to growth in the coffee machine industry, innovation has always been a core pillar of Gruppo Cimbali’s company philosophy. Investing in the research and development of high-performance machines is a strategic decision, and Gruppo Cimbali is proud to be recognized as one of the first companies in the sector to expand into telemetry, Internet of Things (IoT), and Wi-Fi connected machines. To continue to deliver on its innovation promise, the company now applies digital twins – utilizing Altair Activate® – to their development processes enabling it to design better products, shorten development times, and increase energy efficiency.

Digital Twin Implementation: A Strategic Tool to Improve Process/Product Capabilities in Sheet Metal Forming
Sheet Metal Forming has different and wide industrial applications (Automotive, White Goods, Aeronautic, etc....). In the metal forming industry, the simulation of processes and the resulting material behavior is of high importance. Important process parameters (e.g., material flow, temperature range, force required), as well as the resulting material characteristics (e.g., strength, residual stress, temperature resistance), can be supported using FEA to replace costly and uneconomical practical tests.
The re-use of knowledge gained from these FEA simulations in combination with data provided by different sensors is the next step towards the implementation of a Digital Twin. Its integration into the IT architecture of a digital factory is inevitable to increase the efficiency and environmental sustainability of processes and products in manufacturing. Therefore the presented project relies on Reduced Order Models in use of Machine Learning approaches as well as an IoT-based dashboard for the combined visualization of actual data and derived KPIs. As a result, the implemented solution enables significant improvement of capabilities in the considered context.

Digital Twin Platform for Optimized Product Performance | Altair
Digital twins help organizations optimize product performance, gain visibility into the in-service life of a product, know when and where to perform predictive maintenance, and how to extend a product’s remaining useful life (RUL). The Altair digital twin integration platform blends physics- and data-driven twins to support optimization throughout the products lifecycle. We take a complete, open, and flexible approach that enables your digital transformation vision on your terms.